다점 평탄도 검사 과제를 해결하는 측정 방법
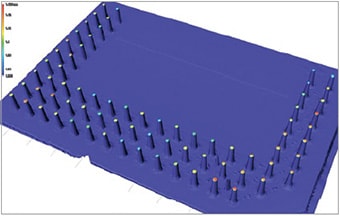
자동차의 전자제어화의 발전과 스마트폰, 웨어러블 디바이스 등의 보급과 소형화 등을 배경으로 이들에 탑재되는 전자 부품의 소형화·고밀도화에 대한 요구가 높아지고 있습니다.
한편, 소형이면서도 고밀도로 조립된 전자기기에서는 작은 부하에도 실장 기판이나 표면 실장 디바이스 접속부의 들뜸 등에 의해 결함이 생기는 경우가 있습니다. 특히 자동차나 항공기는 인명에도 연관이 있기 때문에 소형화와 더불어 IC칩 등의 반도체 패키지의 표면 실장 디바이스(SMD)나 커넥터의 핀 등의 접속 품질을 추구할 필요가 있습니다. 여기서 중요한 것이 다점 평탄도 검사입니다.
여기에서는 전자 디바이스의 실장 품질에 크게 관련되는 리드나 핀, 볼 등 접속 부분의 다점 평탄도의 기초 지식이나 측정 방법, 측정 과제와 최신 개선 방법에 대해 설명합니다.
- 다점 평탄도란?
- 다점 평탄도 측정의 중요성과 품질에 미치는 영향
- 기존의 다점 평탄도 측정 과제
- 다점 평탄도 측정 과제 해결 방법
- 요약: 어려웠던 다점 평탄도 측정을 비약적으로 개선·효율화
다점 평탄도란?
다점 평탄도(coplanarity)란 여러 개의 점이 동일 평면상에 존재하는 성질이나 상태를 의미하는 말입니다. 표면 실장 디바이스나 커넥터 등 전자 부품에 있어서의 다점 평탄도란 PGA의 핀이나 BGA의 땜납 볼, 커넥터의 커넥터 핀 등의 접촉점이 가장 높은 부분과 가장 낮은 부분 사이의 최대치를 나타냅니다. 「면 균일성」이나 「단자 평탄도」라고도 불립니다.
예를 들어 완전히 평탄한 기판 표면을 기준선으로 하고 거기에 표면 실장 디바이스를 놓았을 때 허용되는 다점 평탄도의 값은 기판 표면과 핀 또는 땜납 볼의 복수 접촉점 사이의 최대 단차이며 공차로 정의됩니다.또한 혼동되기 쉬운 요소로 「스탠드 오프」가 있습니다. 이것은 기판 장착면과 디바이스의 패키지 본체(몰드)의 밑면까지의 거리를 나타냅니다.
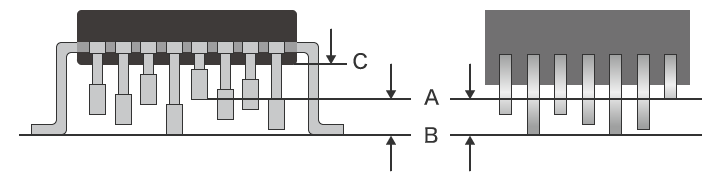
- A
- 다점 평탄도
- B
- 기준선
- C
- 스탠드 오프
다점 평탄도 측정의 중요성과 품질에 미치는 영향
전자 부품의 접촉점에 허용 범위(공차) 외의 단차가 있을 경우 전자 디바이스의 기판 실장시에 접속 불량이나 커넥터의 접촉 불량이 생기거나 사용시의 약간의 부하가 접속 불량 등 의 원인이 될 수 있습니다.
전자 부품의 핀, 땜납 볼, 리드 등의 접속 부분의 다점 평탄도를 측정·검사하는 것은 부품 그 자체의 품질, 조립시의 품질, 그리고 출하 후의 시장에서의 신뢰성까지 이어집니다.
특히 실장 기판이나 디바이스에 부하가 걸리면 육안으로는 보이지 않는 크랙이나 패키지 균열 등의 문제가 발생합니다. 또한 핀이나 리드 등의 선단부 등은 땜납 접합부가 뜨는 문제도 생깁니다. 게다가 패키지 부하에 의해 수지부 등에 약간의 통기구가 생김으로써 내부 부식의 원인이 되는 케이스도 있습니다.
핀이나 땜납 볼, 리드 등의 접점 부품은 프레스 가공·소성 가공·단조 가공·절삭 가공 및 수지로 덮는 등의 공정을 거쳐 제조되기 때문에 기계적 또는 열 스트레스를 받습니다. 그러므로 다점 평탄도는 단지 그 2차원적인 치수 계산만으로는 도면과 같은 형상으로 제조되었다고 판단할 수 없는 경우가 있습니다. 기울기나 굽힘 등 3차원적인 형상 변화에 의해서도 피치나 다점 평탄도의 편차가 생겨 접속 불량의 원인이 됩니다.
기존의 다점 평탄도 측정 과제
기존의 다점 평탄도 측정 방법과 그 과제에 대해 설명합니다.
틈새 게이지에서의 다점 평탄도 측정 과제
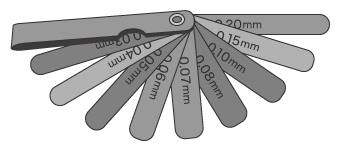
틈새 게이지란 금속의 얇은 판을 틈새에 넣어 치수를 측정하는 측정 공구입니다. 시크니스 게이지라고도 합니다. 일반적으로 0.03~1.00mm까지의 좁은 틈을 측정할 수 있습니다.
틈새 게이지를 이용한 측정에는 다음과 같은 과제가 있었습니다.
- 수동으로 대상 물체(IC 패키지의 리드 프레임 등)를 접촉시켜 틈새를 측정합니다. 그러나 이 방법에서는 측정값의 편차가 크고 신중하게 취급하지 않으면 전자 부품이 파손됩니다. 측정·검사에는 많은 수고와 시간이 걸리므로 전수 검사는 어렵습니다.
- 측정 결과를 데이터로 출력할 수 없기 때문에 리포트를 작성하거나 불량률의 경향 등을 분석하기 위해서는 우선 손으로 데이터를 입력해야 합니다.
현미경에서의 다점 평탄도 측정 과제
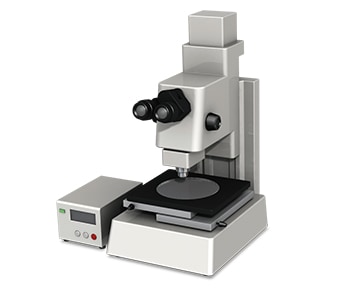
금속 현미경이나 실체 현미경을 바탕으로 하여 측정용으로 개발된 측정 현미경은 1μm 정도의 측정 정밀도를 구현할 수 있습니다. 또한 스테이지의 이동량을 수치로 확인할 수 있습니다.
현미경을 사용한 측정에서는 다음과 같은 과제가 있었습니다.
- 측정 방향에 제한이 있기 때문에 입체적으로 배치된 여러 개의 핀을 측정하기 위해서는 지그를 이용하여 대상 물체를 다양한 방향으로 고정하여 측정해야 하기 때문에 시간이 걸렸습니다.
- 치수를 육안으로 확인해야 하기 때문에 측정하는 사람에 따라 오차가 발생했습니다.
다점 평탄도 측정 과제 해결 방법
기존에 사용되고 있는 일반적인 측정 기구나 현미경에서는 다점 평탄도를 측정·검사하기에는 많은 수고와 시간이 필요할 뿐만 아니라 측정값의 편차가 발생하는 큰 과제가 있었습니다. 또한 접촉식의 측정 기구에서는 소형화되는 전자 디바이스의 측정이 어려울뿐 아니라 측정 시 대상 물체가 파손될 우려도 있었습니다.
이러한 측정 과제를 해결하기 위해 KEYENCE에서는 원 샷 3D 형상 측정기「VR 시리즈」를 개발했습니다.
「VR 시리즈」는 대상 물체의 3D 형상을 비접촉으로 평면에서 정확하게 포착합니다. 스테이지의 대상 물체를 최고 속도 1초만에 3D 스캔하여 3차원 형상을 고정도로 측정할 수 있습니다. 그 때문에 측정 결과의 편차 없이 순식간에 정량 측정·검사할 수 있습니다. 여기에서는 구체적인 장점을 소개합니다.
장점 1: 신속하고 간단하게 형상 측정이 가능
「VR시리즈」는 대상 물체를 스테이지 위에 올리기만 하면 OK. 자동으로 스테이지를 이동하고 위치를 맞추며 순간적으로 형상을 스캔하는 간단한 조작을 실현했습니다. 이로 인해 측정 항목의 차이 등으로 인한 측정값의 편차가 발생하지 않습니다.
또한 적합한 지그의 선택과 대상 물체 고정 등의 사전 설정 없이 여러 핀이나 리드, 땜납 볼의 다점 평탄도와 형상을 일괄적으로 측정할 수 있으므로 측정에 걸리는 시간을 비약적으로 단축할 수 있습니다.
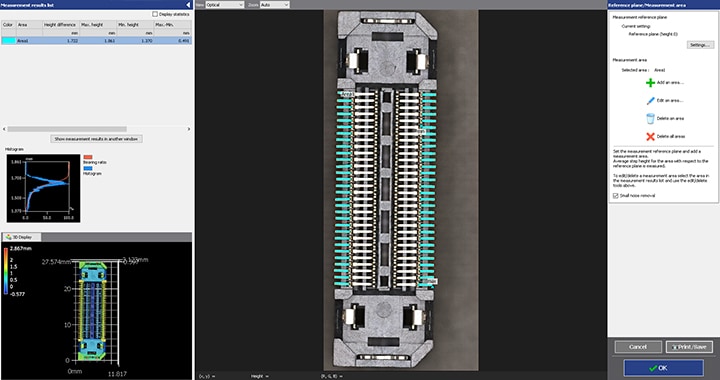
장점 2: 3D 형상을 가시화. 원활한 데이터 활용을 실현
「VR 시리즈」는 대상 물체의 면 전체의 3D 형상을 스캔하여 데이터화하기 때문에 시각적으로 알기 쉬운 화상 데이터를 출력하는 것이 가능합니다.
예를 들어 다수의 줄지어 있는 핀이나 리드의 구부러짐 및 기울기로 인한 높이 차이를 일괄적으로 포착해 그 차이를 색으로 구분한 3D 화상 등으로 표현할 수 있습니다. 이로 인해 대상 물체의 어느 부분의 다점 평탄도가 공차를 벗어났고 어떠한 형상이 문제를 초래하고 있는지를 구체적으로 파악할 수 있어 불량 원인의 발견과 재발 방지에도 도움이 될 수 있습니다. 또한 이러한 이미지 데이터를 이용하여 이해하기 쉬운 리포트를 간단히 작성하거나 다른 부서와 정보를 공유할 수 있습니다.
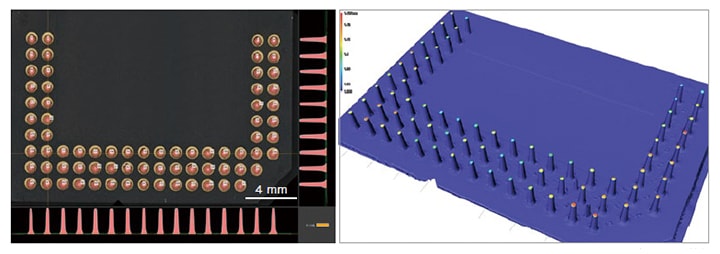
요약: 어려웠던 다점 평탄도 측정을 비약적으로 개선·효율화
「VR 시리즈」라면 비접촉으로 순식간에 대상 물체의 3D 형상을 면으로 스캔하여 측정할 수 있습니다. 전자 부품의 다점 평탄도 측정은 기존 측정 과제를 해결할 뿐만 아니라 업무 효율도 비약적으로 향상시킵니다.
- 비접촉이기 때문에 섬세한 전자 부품이 측정압 등으로 파손될 우려가 없습니다.
- 스테이지에 대상 물체를 올리기만 하면 OK. 자동으로 위치를 결정하여 측정할 수 있으므로 측정값의 편차가 없고, 신속하게 검사할 수 있습니다.
- 다수의 줄지어 있는 핀이나 리드, 땜납 볼의 다점 평탄도를 순식간에 일괄적으로 측정할 수 있습니다.
- 3D화상으로 높이의 차이를 색으로 나누어 표시하는 등, 시각적으로 알기 쉬운 화상 데이터를 출력할 수 있으며. 이해하기 쉬운 리포트의 작성도 간단합니다.
기존 전자 부품의 측정 과제를 클리어하고 대상 물체를 면으로 순식간에 일괄 측정할 수 있는 「VR 시리즈」는 전자 부품의 소형화·고밀도화라고 하는 현대의 요구에 대응하면서도 측정이나 리포트 작성에 소요되는 공정 수나 작업 효율을 대폭 향상시킬 수 있습니다.