휨의 측정 방법과 효율화의 비결
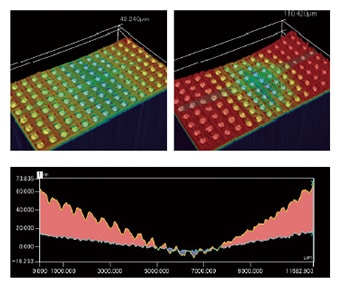
평면의 휨을 측정하는 측정기로는 다이얼 게이지나 형상 측정기, 3차원 측정기 등이 있습니다. 그러나 휨은 입체적인 변형이기 때문에 점이나 선으로 측정하는 기존의 측정 방법으로는 휨을 정확하게 측정하는 것이 어려웠습니다.
대상 물체의 형상이나 사이즈에 따라 기존의 방법으로는 휨을 정확하게 측정할 수 없는 부분이 생기거나 물리적으로 측정 자체가 불가능한 부분이 발생하는 경우가 많이 있습니다.
여기에서는 휨의 기초 지식과 측정 방법, 기존의 측정 과제 그리고 새로운 해결 방법에 대해 소개합니다.
휨이란?
휨이란 말 그대로 물체가 활처럼 구부러져 있는 상태를 가리키는 말입니다. 일반적으로 공업제품에서의 휨은 판 형태를 한 대상 물체의 굴곡을 말하며, 「평면도(평평한 정도)」가 규정의 공차값을 초과하고 있는지 그 여부를 가리킵니다.
평면도(平面度)란?
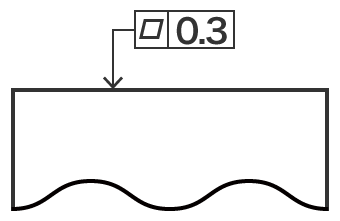
평면도는 「판 면의 완곡이나 물결 모양의 틀어진 정도」로 정의되어 있습니다. 도면으로 나타내면 다음과 같습니다.
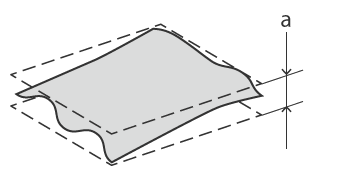
- A
- 0.3mm 이하
완벽하게 평평한 두 개의 평면 사이에 대상물을 끼웠다고 가정했을 때, 두 개의 평면 사이의 폭이 나타내는 값을 평면도입니다. 즉 대상 물체가 얼마나 평평한 면이어야 하는가에 대한 공차를 지정하고, 물체의 가장 튀어나온 부분과 가장 함몰된 부분이 상하로 분리된 두 평면 사이의 일정 거리에 있어야 한다는 것입니다.
위 도면이 나타내는 평면도의 공차 지정 이미지는 다음과 같습니다.
휨 발생 원인과 영향
제품·부품의 휨은 재질이나 제조·가공 방법에 따라 다양한 원인과 영향이 있습니다. 그 예는 다음과 같습니다.
수지 성형품의 휨
수지(플라스틱) 성형에서는 수지 재료의 고화 시에 발생하는 수축차나 금형의 냉각 온도차, 재료 배향 등이 원인이 되어 성형품에 휨이 생깁니다.
또한 사출 성형의 경우 사출·보압의 시간이나 압력 등이 휨의 원인이 되는 경우가 있습니다.
웨이퍼 휨
웨이퍼는 각 공정에서 스트레스(기계적 응력)를 받습니다. 대부분의 경우 이러한 스트레스가 웨이퍼 앞뒤에 불균형하게 가해지면서 휨이 발생합니다. 특히 연마 공정에서는 가공면에 대한 응력이 강한 경우 잔류 응력에 의해 볼록한 휨(순방향 휨) 또는 오목한 휨(역방향 휨)이 발생할 수 있습니다.
웨이퍼에 휨이 있는 경우 칩 불량이 발생하는 것 외에도 핸들링 시의 진공 누설에 의한 흡착 부족으로 웨이퍼가 낙하하는 등의 문제를 일으켜 수율에 영향을 주는 경우가 있습니다.
프린트 기판의 휨
전자 부품의 소형화·고밀도 실장화가 진행됨에 따라 리플로우 방식에 의한 실장이 일반화되었습니다. 그러나, 리플로우 실장 공정에서의 가열이 원인이 되어 기판에 휨이 생기는 경우가 있습니다.
리플로우 가열 시 기판에 휨이 발생하면 실장한 IC 리드에 들뜸이 생겨 실장 불량·접속 불량을 초래하는 경우가 있습니다.
또한 실장 후의 통전·사용 시의 발열에서도 기판이 휘어져 버리는 경우가 있고 이에 따라 부품의 접점에 결함이 생겨 고장의 원인이 되는 경우가 있습니다.
금속판의 휨
프레스 등 각종 금속 가공 시에 가해지는 열이나 잔류 응력은 대표적인 휨의 발생 원인입니다.
그러나 와이어 방전 가공 등으로 금속판을 추출하는 프레스 가공용 플레이트 부자재 자체의 평면도가 유지되어 있지 않으면 가공 후 제품의 형상에 영향을 미칩니다. 금속 부자재는 부재는 열팽창에 의해서도 휨이 생기기 때문에 부자재의 보관 온도 외에 지그·가공기의 온도를 고려하는 것 중요합니다.
휨 측정의 중요성과 과제
앞서 언급한 휨 발생의 예 이외에도 열이나 잔류 응력 등에 의해 휨이 발생하는 경우는 적지 않습니다. 불량 발생이나 고장 등을 방지하고 높은 품질을 유지하기 위해서는 가공 전의 부자재나 가공 후 제품의 휨을 정확하게 측정하는 것이 중요합니다.
휨의 측정 방법은 다음과 같이 다양합니다.
- 암에 다이얼 게이지를 고정하고 대상 물체를 덧그리면서 수치의 변화를 읽는 방법.
- 평평한 측정면을 가진 투명한 유리제의 기준 원기, 옵티컬 플랫을 접촉시키면서 줄무늬(광파 간섭 무늬: 뉴턴 링)의 개수로 측정하는 방법.
- 윤곽 형상 측정기나 3차원 측정기 등을 사용한 측정 방법.
그러나 기존의 접촉식 측정기를 이용한 휨의 측정에는 다음과 같은 과제가 있었습니다.
윤곽 형상 측정기를 이용한 휨 측정 과제

윤곽 형상 측정기란 스타일러스라고 하는 프로브를 이용하여 대상 물체의 표면을 덧그림으로써 그 윤곽 형상을 측정, 기록하는 장치입니다.
최근에는 프로브 대신 레이저를 이용하여 비접촉 방식으로 윤곽을 스캔함으로써 복잡한 형상의 측정에 대응할 수 있는 기종도 있습니다. 또한 기종에 따라서는 상하 양면의 측정이 가능한 것도 있습니다.
윤곽 형상 측정기를 이용한 휨 측정에서는 다음과 같은 과제가 있었습니다.
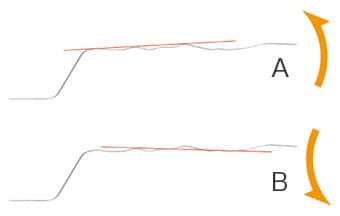
- A
- 우상향
- B
- 오우하향
- 대상 물체를 선으로 덧그리며 측정하므로 휨을 파악할 수 없습니다.
- 대상 물체에서 표면 전체가 어떤 상태인지 파악할 수 없습니다.
- 표면 실장 후의 기판과 같이 본래 측정하고 싶은 면 이외에 요철(칩)이 있는 경우, 휨의 유무 여부를 측정하는 것이 어렵습니다.
- 선의 기준면 설정이 어려우므로 측정 오차가 발생할 수 있습니다(그림).
3차원 측정기를 이용한 휨 측정 과제
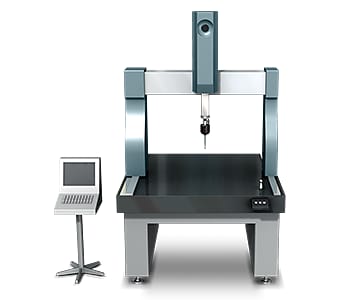
일반적으로 3차원 측정기로 휨을 측정하려면 대상 물체에서 측정하고 싶은 면의 모서리 4개 이상에 프로브 선단의 접촉자를 맞추어야 합니다.
예를 들어 플레이트 부재의 경우 6~8지점을 측정하는 것이 일반적입니다. 측정 범위가 넓을 경우 측정 항목을 늘려 더 많은 부분의 측정값을 얻는 것으로 측정 정도를 향상시킬 수 있습니다.
휨 측정에서는 다음과 같은 과제가 있었습니다.
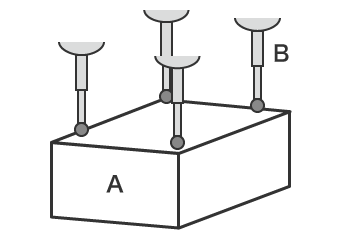
- A
- 대상 물체
- B
- 프로브
- 점으로 접촉하여 측정해야 하기 때문에 기본적으로 전체 형상을 얻기 어렵습니다.
- 보다 많은 측정값을 얻기 위해 다점 측정을 하기에는 많은 시간이 걸리며 전체 형상을 상세하게 파악할 수 없습니다.
휨 측정의 과제 해결 방법
기존의 접촉식 계측기는 점이나 선으로 형상을 측정하기 때문에 측정하고자 하는 대상 물체의 면 전체를 측정할 수 없었습니다. 또한 측정 정도를 향상시키기 위해서 다점 측정을 진행한다 하더라도 휨을 포함한 정확한 형상을 파악하는 것이 어려운 데다가 많은 공정 수가 요구됩니다. 또한 대부분의 경우, 휨 측정에는 경험, 지식 및 기술이 필요합니다. 뿐만 아니라 측정할 수 있는 인원의 확보나 사람에 따른 측정값의 편차도 큰 과제였습니다.
이러한 측정 현장의 과제를 해결하기 위해 KEYENCE에서는 원 샷 3D 형상 측정기 「VR 시리즈」를 개발했습니다.
「VR 시리즈」는 대상 물체에서 3D 형상을 비접촉 방식으로 면에서 정확하게 포착합니다. 정밀한 위치 결정이 필요 없고 스테이지에 놓인 대상 물체를 최고 속도 1초 만에 3D 스캔하여 3차원 형상을 고정도로 측정할 수 있습니다. 이로 인해 측정 결과의 편차 없이 정량적인 측정·검사를 신속하게 진행할 수 있습니다. 여기에서는 구체적인 장점을 소개합니다.
장점 1: 면으로 형상을 스캔하여 전체 형상을 순식간에 파악
예를 들면 프레스 가공 중에서도 조건 설정의 난이도가 높은 「드로잉 가공」은 기계적 응력에 의해 재료에 의도하지 않은 변형이 생길 수 있어 휨 등의 형상 불량 발생에 주의할 필요가 있습니다.
「VR 시리즈」를 사용하면 스테이지 위에 대상 물체를 놓고 스캔하기만 하면 됩니다. 위치 결정이 필요 없고, 대상 물체 전체의 3D 형상을 면으로 포착합니다.
대상 물체 전체의 높이를 색으로 구분하여 표시하거나, 임의로 지정한 부분에 대한 프로파일 측정도 가능하기 때문에 형상 불량 부분과 그 상세한 수치 등을 가시화하여 파악할 수 있습니다. 이에 따라 금형이나 성형 조건 등 불량 원인의 특정 및 조정도 원활하게 실시할 수 있습니다.
또한 정량적으로 측정한 형상 데이터를 얻을 수 있기 때문에 이를 활용하여 허용값(공차)의 수치로 휨을 관리하거나, 경향 분석을 진행할 수 있습니다.
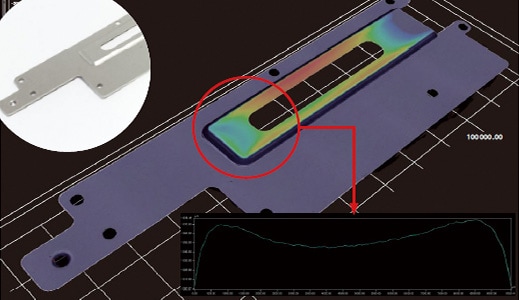
장점 2: 비접촉, 최고 속도 1초의 고속 스캔으로 전체의 휨도 쉽게 파악
기판은 리플로우 공정에서의 가열에 의해 휨이 생길 수 있어 리드 들뜸 등의 원인이 됩니다. 그러나 기존의 접촉식 측정기에서는 표면 실장 후 기판 전체의 휨을 측정하기 어려웠습니다.
「VR시리즈」를 사용하면 실장 후의 기판도 스테이지 위에 올려 최고 속도 1초 만에 전체 형상을 비접촉 방식으로 스캔할 수 있어 기판 전체의 휨은 물론 실장 부품의 들뜸도 순식간에 파악할 수 있습니다. 게다가 불량 부분 등 임의로 지정한 부분의 프로파일 데이터를 취득할 수 있기 때문에 형상 변화의 상세한 데이터를 신속하게 취득할 수 있습니다.
대상 물체의 정밀한 위치 결정은 필요하지 않습니다. 대상 물체를 스테이지에 두는 것만으로 자동적으로 이미지를 보정하기 때문에 정량적인 측정·검사를 빠르고 간단하게 실시할 수 있습니다.
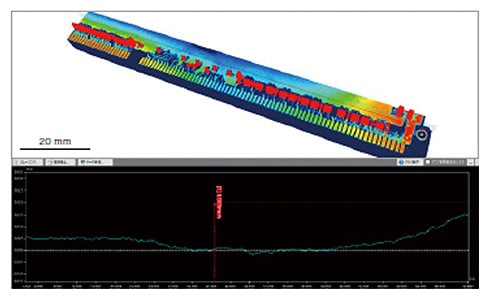
장점 3: 여러 개의 측정 데이터로 정량적인 비교·해석이 가능
최고 속도 1초만에 대상물 전체의 3D 형상을 면으로 스캔하여 측정할 수 있는 「VR 시리즈」는 기존에 비해 단시간에 많은 대상물을 정량적으로 측정할 수 있습니다. 이렇게 효율적으로 수집한 여러 측정 데이터는 목록으로 표시할 수 있는 것은 물론 모든 데이터에 같은 해석 내용을 일괄적으로 적용할 수 있습니다.
이를 통해 여러 대상 물체에서 형상 데이터의 차이를 한눈에 확인할 수 있습니다. 예를 들어 여러 데이터의 평면도를 일괄 분석하여 정상 제품과 비교해 불량품에 어느 정도의 휨이 있는지 정량적인 평가를 빠르고 간단하게 할 수 있습니다.
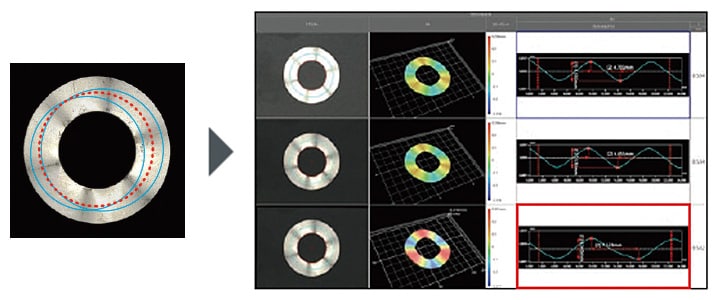
- 왼쪽
- 기존 측정기… 측정 부분의 어긋남·측정값의 편차에 따라 정확한 비교가 어렵습니다.
- 오른쪽
- VR시리즈… 위치 결정이 불필요하여 순식간에 측정. 여러 개의 측정 결과를 나열해 동일한 해석 내용을 일괄 적용할 수 있어 정량적인 비교·해석을 간단하게 진행 가능.
요약: 측정하기 어려웠던 휨 측정을 비약적으로 개선 · 효율화
「VR 시리즈」를 사용하면 고속 3D 스캔을 통해 휨 등을 포함한 대상 물체의 정확한 3D 형상을 비접촉 방식으로 신속하게 측정할 수 있습니다.
- 면으로 포착하기 때문에 대상 물체 전체에서 휘어져 있는 부분을 파악하고 임의로 지정한 부분의 프로파일 측정을 할 수 있습니다.
- 위치 결정 없이 대상 물체를 스테이지에 놓고 버튼을 누르기만 하면 되는 간단한 조작으로 측정을 할 수 있습니다.
- 간단·고속·고정도로 3D 형상을 측정할 수 있으므로 단시간에 많은 대상 물체를 측정할 수 있습니다.
- 여러 측정 데이터의 정량적인 비교·해석을 간단하게 할 수 있습니다.
그 밖에도 평면도의 공차를 설정하는 것으로 정상/불량품의 판별을 진행하거나, 데이터를 활용한 불량품의 분석을 간편하게 실시할 수 있습니다. 실장 기판 등 기존에는 불가능했던 대상 물체의 휨 측정이 가능하므로 신속하고 정확한 휨 측정 그리고 측정 작업의 비약적인 효율화와 원활한 데이터 해석을 해석이 가능합니다.