화학·재료·소재 업계
디지털 마이크로스코프를 이용한 코팅의 관찰·측정
필름이나 시트, 강판, 글라스 등의 비교적 얇은 기재(대상 물체)에 대해 새로운 기능을 부여하는 가공은 「컨버팅」이라고도 합니다. 일반적으로 도포(도공)·증착·스퍼터링 등의 방법으로 이를 실행하는 것을 「코팅」이라 합니다. 스마트폰이나 태블릿 단말기에서 수요가 많은 터치 패널의 전극, 액정 글라스나 필름의 박막 코팅, 전자 기판에 대한 정밀 패턴 도포 등 다양한 분야에서 활용되고 있습니다. 여기에서는 디지털 마이크로스코프를 이용한 코팅의 관찰·측정 사례를 소개합니다.
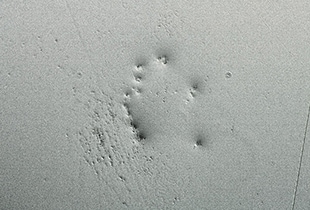
도금과 코팅의 차이
- 도금
- 소재를 금속으로 피복하여 금속을 도전성 표면으로 피막하는 전기 도금이 일반적입니다. 화학 반응을 이용하는 화학 도금, 용융 금속 안에 담가 피막을 형성하는 용융 도금, 금속의 증기에 노출시켜 피막을 형성하는 증착 도금 등도 있습니다.
- 코팅
- 소재를 다른 재질로 피복하여 도전성 표면과 비도전성 표면 양쪽으로 피막을 형성합니다. 코팅에 도금도 포함된다고 볼 수 있습니다.
코팅의 목적
- 기능 부여
- 기재(대상 물체)에 대해 접착성, 습윤성, 발수성, 내식성, 내열성, 내마모성 등의 기능을 부여할 수 있습니다.
- 표면 처리
- 기재의 표면을 최적화하기 위해 약제를 도포하여 「표면 처리」를 할 수도 있습니다. 예를 들면 반도체 웨이퍼에 레지스트를 도포하기 전 약제를 도포하여 소수 가공을 하는 경우가 있습니다.
- 장식성(디자인성)
- 외관(디자인성)을 향상시키는 효과가 있습니다.
코팅의 종류
- 드라이 코팅(건식법)
- 기능 부여를 위한 물질을 「고체」 상태 그대로 기재에 코팅하는 기술을 총칭하여 「드라이 코팅(건식법)」이라고 합니다. 대표적인 코팅 방법으로는 진공 증착이나 이온 플레이팅, 스퍼터링 등이 있습니다. 금속 재료 등의 코팅에 이용되고 건조 공정이 필요 없으며 고품질의 성막이 가능하지만, 장비의 대형화나 연속 생산 수 제한, 고비용이라는 단점도 있습니다.
- 웨트 코팅(습식법)
- 광범위한 공업 분야에서 일반적으로 이용되며 「도포(도공)」에 큰 영향을 미치는 것이 「웨트 코팅」입니다. 기능 부여를 위한 물질을 용매에 용해 또는 분산 처리하여 「액체화」합니다. 그 액제를 기재에 균일하게 도포하고 건조 또는 경화를 통해 「고체 박막화」시키는 기술입니다. 액막에 먼지나 이물질이 부착되지 않게 하려면 웨트 프로세스 시 클린 룸을 사용합니다. 드라이 코팅과 달리 진공 환경이 필요 없고 대기 중에서 도포(도공)가 가능합니다. 장비의 자유도가 높고 대상 물체(기재)를 연속적으로 공급할 수 있습니다. 웨트 코팅은 양산에서의 장점이 크기 때문에 여러 가지 도포 방법을 이용하여 널리 채택되고 있습니다.
디지털 마이크로스코프를 이용한 코팅 관찰·측정 사례
KEYENCE의 4K 디지털 마이크로스코프 「VHX 시리즈」를 이용한 코팅의 최신 관찰·측정 사례를 소개합니다.


HDR로 결점을 가시화할 수 있습니다.


Optical Shadow Effect Mode(컬러 맵) 화상
Optical Shadow Effect Mode 기능을 사용하여
요철을 가시화할 수 있습니다.

VH-Z20 200× 동축 낙사 조명
- A: 일반 화상
- B: 미분 간섭+HDR 화상
미분 간섭+HDR로 도장 얼룩을 가시화할 수 있습니다.

VH-Z20 100× 링 조명
- A: 일반 화상
- B: 심도 합성 화상
투명한 코팅막의 표면도 관찰할 수 있습니다.


자동 면적 계측으로 코팅 입자의 편차를 정량화할 수 있습니다.



코팅막 내부에 이물질이 있는 것이 확인되었습니다.