사출 성형이란
1. 개요와 특징
사출 성형은 금형을 이용한 성형법 중 하나입니다. 합성 수지(플라스틱) 등의 재료를 가열해서 녹이고 금형에 주입한 뒤 냉각시켜 원하는 성형을 실행합니다. 주사기로 액체를 주입하는 모습과 유사하다는 점에서 「사출 성형」으로 불리게 되었습니다. 가공 과정은 재료를 「녹이기」부터 시작하여 「흘리기」「굳히기」「꺼내기」「마무리 가공」의 순서로 이루어집니다.
사출 성형은 복잡한 형상을 포함해 다양한 형태의 부품을 연속해서 신속하게 대량으로 제조할 수 있습니다. 따라서 일용품을 비롯한 폭넓은 분야의 제품에 이용되고 있습니다.
2. 사출 성형기
사출 성형기는 서보 모터로 작동하는 전동식과 유압 모터를 이용한 유압식, 서보 모터와 유압 모터를 조합한 하이브리드식 등이 있습니다. 기계의 주요 구조는 재료를 녹여 금형 내부에 주입하는 「사출부」와 금형을 세팅하는 「형체부」로 구성되어 있습니다.
최근에는 사출 성형기의 CNC화가 진행되어 컨트롤러의 제어를 기반으로 고속 사출할 수 있는 장비들이 보급되었습니다. 또한, 액정 모니터의 도광판을 전문으로 성형하는 장비 등 특수한 용도의 전문 장비들도 다수 출시되고 있습니다.
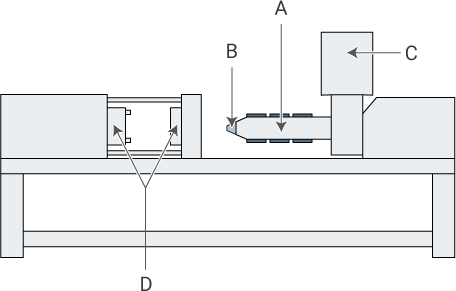
- A
- 실린더(재료 가열부)
- B
- 노즐(액화된 재료를 사출)
- C
- 호퍼(재료 투입구)
- D
- 금형(양쪽 금형이 맞닿는 사이에 재료를 부어 넣는다)
3. 사출 성형을 이용한 가공
사출 성형을 이용해 가공하려면 먼저 재료의 투입구인 호퍼에 펠릿(알갱이) 형상의 수지를 넣습니다. 펠릿이 실린더 안에서 가열되어 액상으로 변하면 사출 준비가 갖추어집니다. 그리고 사출부의 노즐에서 배출된 재료는 금형 내의 스프루라는 관로를 통과하고 다시 분기된 러너를 지나 성형 부분으로 흘러들어갑니다. 재료가 냉각되고 고화된 후에 금형이 열리고 성형품이 외부로 배출됩니다. 그런 다음, 마무리 가공으로 스프루 및 러너가 절단되고 성형 부분이 완성됩니다.
실제로는 사출 성형 한 번으로 여러 개의 성형품을 동시에 제조하는 경우가 많으므로 용융된 재료가 모든 부위에 균등하게 흘러들어가는 것이 중요합니다. 따라서 러너의 길이를 동일하게 하는 등 금형 형상을 세심하게 고려하여 설계해야 합니다.
사출 성형은 대량 생산에 적합한 가공 기술이지만 정도 높은 성형품을 생산하려면 재료인 수지의 선택부터 금형의 가공 정도, 재료 사출 시의 온도나 속도 등 다양한 조건을 숙지해 두어야 합니다.
용융된 재료의 주입구
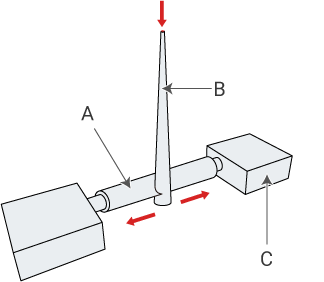
성형 후 러너를 분리하여 완성
- A
- 러너
- B
- 스프루
- C
- 성형부